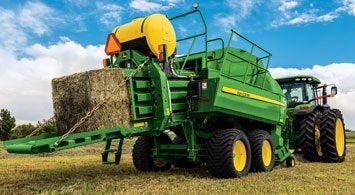
Baling hay is a process that has come along a lot since the late 1800s when Cyrus McCormick commercialized a reaper design using a knotter to bundle and bind hay. This was a big improvement on the manual hay rake, and allowed more efficient and safer storage than the haystack storage system of the day. The goal, though, was the same: a method of safely storing hay so that it could dry and cure – while retaining nutrients – for livestock feed at a later date.
Today, balers come in a wide variety of sizes and shapes. Some are purely mechanical, and capable of being run by small tractors, while others require the full capabilities of the largest machines fitted with the latest hydraulics and electronics. Choosing the right baler begins with a thorough assessment of the agribusinesses acreage, annual hay production, productivity expectations, equipment available, type of crop, moisture conditions, storage demands, and end usage.
Round or Square?
The first choice to make in selecting a baler is the bales’ physical shape. Square bales (rectangular) dominated farm life for a long time, but round bales these days are now the more common configuration. However, both styles have their advantages and disadvantages.
Round Bale Plusses
• Balers can be run with lower horsepower tractors
• Harder for water to penetrate, so better resistance to weather (rain and dew)
• Can be stored outdoors
• Cattle resistance from fungi and mold in bales stored outdoors is generally greater
• Require less drying time between cutting and baling
• Cheaper initial investment
• Easy handling with bale spears
• Easier feeding out for large herds by running hay out in long strips
• Can generally create higher compaction densities
• Lesser maintenance costs
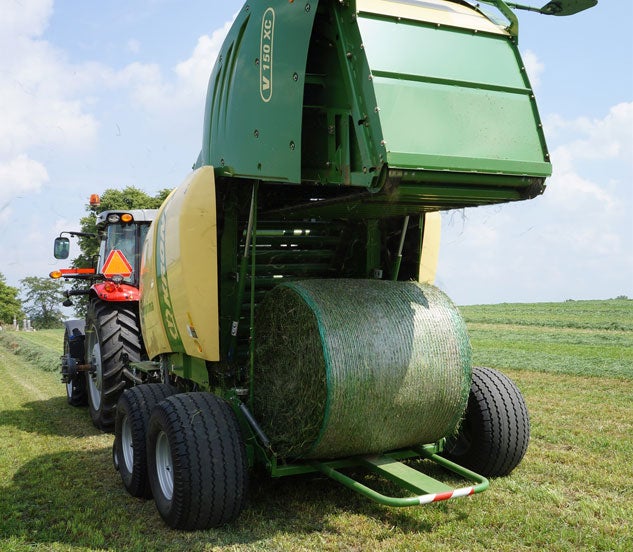
Round Bale Minuses
• Must stop to wrap and unload unless costly continuous baler is used
• Not as good on hills and slopes, plus unloaded bales can roll away through fences or worse
• Not easily stackable
• Not as attractive for resale
• Not easily loaded onto trucks (or safe)
Square Bale Plusses
• Easier to handle and store
• Less prone to mold and fungi (indoor storage)
• Less spoilage
• Easy indoor storage ability protects against precipitation and sunlight and equates to better retention of food value for longer periods of time
• Good marketability for horse owners as horses are more vulnerable to fungi and mold associated with bales stored outdoors (round)
• Easily work with mechanical bale feeders
• Can be operated flat-out (non-stop), pushing out bale after bale (unless knotter skips)
• Bales can be weighed by the baler system if so equipped
• Can easily be tossed into a tow-behind wagon
• Generally, less leaf loss
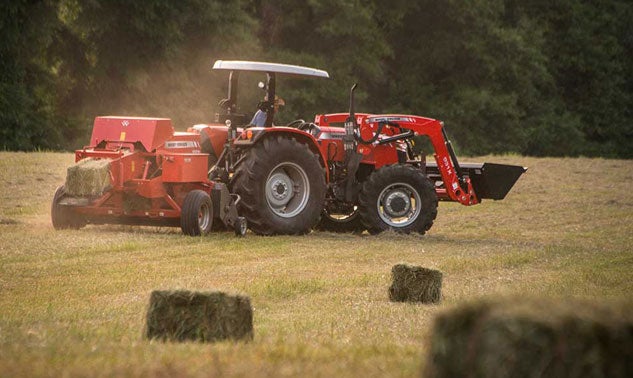
Square Bale Minuses
• Requires more manpower
• Requires more time to dry between cutting and baling (a big minus in wet, cool climates)
• Rain will go right through square bale and ruin it
• Requires more machine horsepower, especially on hilly land
• Cost (can run as much as 3X more than a round baler)
Once the type of baler is chosen, there are some further decisions to make before the purchase. If a square baler is the choice, does the purchaser want to go with an offset baler – that is a baler with the intake chute not directly behind the tractor. Some advantages of an offset baler are that it is a common design favored by many manufacturers, the tractor easily runs in the space between windrows, the sight view of the baler intake chute is preferred by some, and the baler can be run right to the property edge which is preferable to some. The advantages of an inline baler are a less complicated drive system (fewer moving parts), no flight formation adjustment (baler makes square bales), same size tires on both sides, shear bolt easily accessible, possibly less leaf loss due to not having a direction change (jog) especially in dryer than desired conditions.
If a round baler is chosen, that type of system also has some other decisions to make before the purchase. A ground roll round baler uses a pick-up to roll the windrow on the ground where it is formed into a round bale by a series of belts. This now less-commonly used system results in a bale that is of lower density. A fixed volume round baler uses a pick-up to lift the windrow into a chamber waiting until the chamber is full before forming the bale. This type of system results in a bale of greater density than a ground roll baler. More common today is an expandable chamber round baler which also uses a pick-up to lift the windrow into the chamber which expands as the bale forms. Expandable chamber balers form consistently dense bales with the density being greater than ground roll or fixed chamber balers.
The wrap selected is also an important consideration. Generally, there are four types of wrap used: sisal twine, plastic twine, net-wrap, and tube-wrap. Sisal twine will rot when stored outdoors but has an advantage when stored indoors. Sisal twine can also be dropped into a feeder with the twine disappearing. Plastic twine is made from a synthetic polypropylene base and has better rot resistance than sisal twine. Net-wrap is estimated to be 30-35% more productive than twine. The machinery needed does carry a minor cost with an additional ~ $1/bale premium, but often the marketplace will pay a premium for the resultant quality. Net-wrap is best when stored on well-drained surfaces.
Tube-wrap uses a special wrapping unit to wrap the round bales in a continuous line. Typically, a skid-steer or tractor loads the wrapper with bales, while the wrapper wraps the bale then backs away, making room for the next bale. The cost associated with continuous wrapping is less due to the reduced plastic used as-well-as the minimal overwrap. The main disadvantage is that tube-wrapped silage cannot be sold or easily transported. In 2013, John Deere, in a joint venture with Tama, introduced a breathable B-wrap that can be used in place of net-wrap. B-wrap has a layer of breathable film that sheds precipitation but still allows bale moisture to escape through microscopic pores. B-wrap is costly, however, as much as 7X more than sisal twine.
Finally, when baling always follow manufacturer guidelines. We’ll add a few learned over time:
• Typically, the baler pick-up should be set approximately 1” above ground to minimize dirt intake and reduce resultant component wear
• Monitor moisture before baling. Content is critical to results. For large square bales, 12-15% maximum. For small square bales, 18-20%. For round bales, 16-20%. And, never-ever bale when wet
• On the flip side, avoid too-low moisture conditions. Leaf shatter and nutrient losses will occur
• Make sure the operator is properly trained in safe operation and checks to ensure the baled crop is of the highest quality
• Make sure the machinery is at top operating condition. This means following manufacturer-prescribed maintenance intervals
For this article, we’ve chosen to not go into the mowing, conditioning, and windrowing of the crop, but those considerations are equally as important in the quest for the highest quality with the least amount of loss.