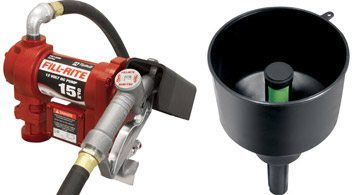
Diesel engines as source of power are some of the most dependable, economical, and long-lasting systems available. Long gone are the days of a bus, truck, or tractor bellowing black smoke from their tailpipes. Tightened EPA emissions standards have challenged manufacturers to improve the combustion process as well as the quality of what goes out in the exhaust stream. Low sulfur diesel (LSD) and ultra-low sulfur diesel (ULSD) fuel have been contributing factors in lowering emissions, but at the same time have also added to the challenges manufacturers face.
In January of 2014, Tractor.com published a Winter Diesel Care feature that touched on some of those issues. Since then, we’ve noticed enough web misinformation to prompt a more detailed piece on what diesel fuel is, how it is influenced by external variables, and what can be done to prevent many trouble issues.
Diesel fuel is petroleum-based and is a less-refined cousin to other common fuels such as gasoline, jet fuel and kerosene. Compared to gasoline, diesel is heavier and oilier, evaporates slower and has a boiling point that is higher than water. A gallon of diesel contains 147,000 BTUs vs. 125,000 for gasoline. Ignition in a diesel engine takes place due to high compression in conjunction with the injection of the fuel and does not need spark as a gasoline engine does. A diesel engine is also highly efficient when throttled down as the air intake is not throttled down like its gasoline counterpart would be.
Waxing On
Diesel fuel contains paraffin (wax) which is good, increasing the cetane number (CN) or content. Cetane is a measure of a fuels’ ignition delay. The benefit of cetane in a diesel is often likened to the performance benefit increased octane brings to a gasoline engine. The minimum cetane requirement in the United States is CN40. A higher CN improves engine starting, especially in cold weather. The primary diesel blends are No. 1, sometimes called 1D and No. 2, sometimes called 2D. No. 2 is considered a summer grade. As cooler weather approaches, distributers change to a winter blend of No. 2 and No. 1.
Diesels: Tractor Engines and the EPA
Fuel stations in cold climates offer two kinds of diesel fuel. Some mix No. 2 with No. 1 kerosene which is a more refined fuel (and more expensive) to make what is known as a winter blend or winter diesel. Some stations may even give their customers a choice of making their own blends, but buyer beware. More common and better for today’s complex fuel systems is winterized diesel, which contains fuel system-healthy additives straight from the refiner. Winterized fuel also costs less to make.
Since diesel fuel contains wax, which as temperatures drop can precipitate out (separate), it is important that a summer blend not be used during the fall-winter-spring cold weather times. A summer blend will begin to have the wax precipitate out around 32F. This first point is known as the cloud point, where the fuel begins to look cloudy.
As temperatures further drop those solidifying wax particles combine into solids that become large enough to clog filters. This second point is known as the pour point or gel point in which so many larger wax particles are present that the fuel no longer flows. The gel point is generally ten to fifteen degrees lower than the cloud point. Kerosene additions lower the gel point. Winterization levels vary across different parts of the country and can range from 10F to as much as -20F, though no real published rating system is in effect or enforced.
Water Issues
The gelling of the wax in diesel fuels at cold temperatures is not the only problem area. Diesel fuels have some water suspended in the mix. At the stage at which wax begins to precipitate out, any water held in suspension will begin to form ice crystals. Add the two together and you have a major problem that can extend from the filter, through the lines and into the tank.
Mahindra mCRD Diesel Technology
Though diesel fuel is relatively free from water from the refinery, water enters the mix through a variety of ways, including in the delivery process, atmospheric variables, from free water settling, condensation and leakage. Generally, these are handling issues, so good practices must prevail. For example, if you receive fuel in bulk, ask to be the first delivery – that way there is less chance of getting water and/or contaminants that have settled to the bottom. The installation of a water removal system at the tank inlet is also effective.
Minimizing atmospheric contamination can take the form of keeping a sealed cap on the tank, can, and/or tractor. And if you’re in an area subject to large temperature swings and high humidity, a water separator can be a helpful line of defense. The trick is to keep the water content below the saturation point.
Zero water in diesel fuel is optimum but not entirely practical. Keeping the water content below the saturation point so it stays dissolved rather than entering the engine as free water is key. To measure water content, a variety of methods can be employed such as an outside lab, water monitors (sensors), and titration testing using the Karl Fischer methodology.
Thunder Creek Equipment and Diesel Exhaust Fluid Handling
To test for settled water at the bottom of a tank, a simple dip test can be effective, requiring just a stick or weighted string to be coated with a water indicating paste and lowered into the tank. If excessive water is found, the tank will have to be drained – a pain and inconvenience to be sure, but the only way to ensure damaging water from reaching your fuel injection system.
Organic Contaminants
Wax and water are not the only areas of concern; bacteria and fungi also like the cool, moist storage environment. On their own, bacteria and fungi have little effect, but their presence leads to acids and corrosive by-products that over time will damage tanks.
To prevent fuel-related trouble, ensure your tractor runs at peak performance when you need it to. To minimize the potential for expensive downtime, we recommend you follow the following steps.
1. Purchase fuel from a reliable outlet. Ensure that fuel is used in a timely manner, understanding that under optimum conditions fuel has a shelf life of six months before significant degradation occurs.
2. Keep your storage tanks, cans, and tractor tank sealed, clean and free from contaminants. Use of a funnel filter while fueling can be beneficial.
3. Store your machines indoors when not being used. Most barns or garages will not be heated, but draping a tarp over the tractor and placing a heat source such as a trouble light near the lines and filter can be helpful. Just don’t do anything that may lead to a fire.
4. Use summer fuel in the summer and winterized fuel in the winter. Additives with cetane boosters can raise lower the gel point protection. Just check your owner manual first to understand manufacturer recommendations.
5. Remember, the three big factors that contribute to fuel contamination are exposure to air, water, and light. Protect against those elements and your fuel system is off to the start it deserves.
Note: Due to the many variables inherent in bio-diesel or bio-fuels, Tractor.com decided those alternates would be better covered in a future piece. Some notable differences are: if a fleet has made a switch to bio-diesel, it won’t be able to use the same fuel treatments since the cloud point will be different; the oils from different vegetables have wide ranges of cetane, with Canola oil having some of the highest; and tractors using high pressure common rail (HPCR) fuel injection systems have specific requirements as to what they can use and what they cannot to avoid costly damage. As always, the manufacturer’s recommendations should be the owner’s first line of defense.